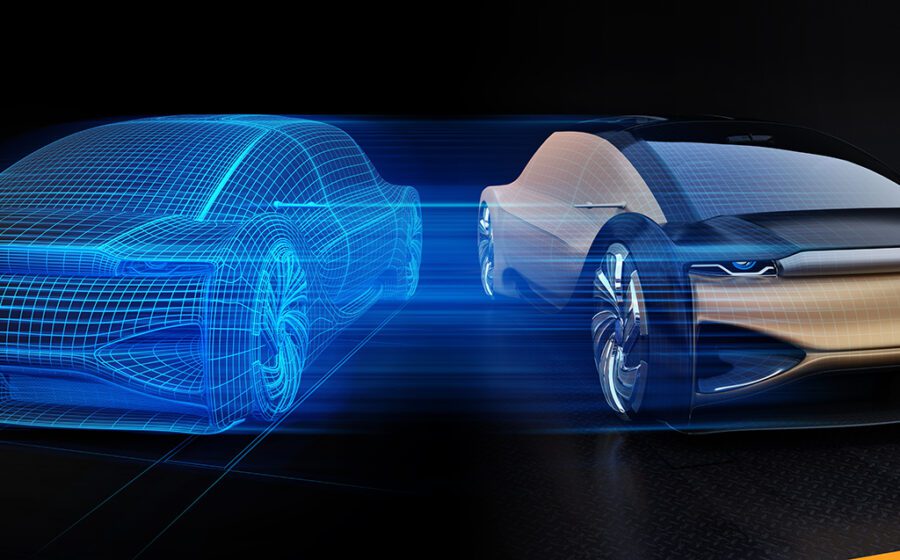
Background
- Digital Twins are virtual representations of physical objects, and they can be connected with their physical counterparts.
- Through this connection, Digital Twins contribute to the convergence of the real and the virtual world.
- While the Digital twin’s concept is focused on the manufacturing industry, the paper “Dimensions of Digital Twin Applications – A Literature Review” analyzes Digital Twin applications across industries.
- In this post, we analyze digital twins across industries along six dimensions based on this paper.
- The twin concept has been known at least since the 1960s. Twins were used for the first time in NASA’s Apollo program.
- Michael Grieves (2014) introduced his concept of “virtual, digital equivalent to a physical product” or “Digital Twin” in 2003. The proposed Digital Twin concept model consists of three main parts: the physical product, the virtual product, and the connection between the physical and the virtual product.
- The digital part not only carries historical data about the physical object but also delivers optimization and predictions.
- Tao et al. (2018) state that a complete Digital Twin should include five parts. They extended the three parts introduced by Grieves by the parts ‘data’ and ‘service’ and emphasized that every part of a Digital Twin is equally important.
Definitions of Digital twins
The paper provides several definitions of digital twins
Tao et al. (2018, p. 2)
“[…A] complete DT [Digital Twin] should include five parts: physical part, virtual part, connection, data, and service.”
Autiosalo (2018, p. 243)
“Digital Twin is the cyber part of a Cyber-Physical System.”
Demkovich et al. (2018, p. 295)
“A Digital Twin of a production system is a multi-level digital layout that describes the product, processes, and resources in the environment of their functioning, i.e., allowing to simulate the processes taking place in the real system, as well as collecting and displaying in real-time data on the status of objects obtained from the PLC and sensors installed in the production system both on industrial equipment and in its environment.”
Kritzinger et al. (2018, p. 1017)
“Based on the given definitions of a Digital Twin in any context, one might identify a common understanding of Digital Twins, as digital counterparts of physical objects.”
Zheng et al. (2018, p. 2)
“In a broad sense, DT [Digital Twin] is an integrated system that can simulate, monitor, calculate, regulate, and control the system status and process.”
Grieves and Vickers (2017, p. 94)
“Digital Twin (DT)—the Digital Twin is a set of virtual information constructs that fully describes a potential or actual physical manufactured product from the micro atomic level to the macro geometrical level. At its optimum, any information obtained from inspecting a physically manufactured product can be obtained from its Digital Twin.”
Negri et al. (2017, p. 946)
“The DT [Digital Twin] consists of a virtual representation of a production system that can run on different simulation disciplines that is characterized by the synchronization between the virtual and real system, thanks to sensed data and connected smart devices, mathematical models, and real-time data elaboration.”
Boschert and Rosen (2016, p. 59)
“The vision of the Digital Twin itself refers to a comprehensive physical and functional description of a component, product or system, which includes more or less all information which could be useful in all—the current and subsequent— lifecycle phases.”
Grieves (2014, p. 1)
“The Digital Twin concept model […] contains three main parts: a) physical products in Real Space, b) virtual products in Virtual Space, and c) the connections of data and information that tie the virtual and real products together.”
Glaessgen and Stargel (2012, p. 7)
“A Digital Twin is an integrated multiphysics, multiscale, probabilistic simulation of an as-built vehicle or system that uses the best available physical models, sensor updates, fleet history, etc., to mirror its life corresponding flying twin. The Digital Twin is ultra-realistic and may consider one or more important and interdependent vehicle systems, including airframe, propulsion and energy storage, life support, avionics, thermal protection, etc.[sic]”
The common denominators are:
- A Digital Twin is a virtual representation of a physical product.
- Some definitions emphasize the connection between the two parts
- whereas others include possible Digital Twins applications such as simulation.
Dimensions of Digital Twin Applications
The paper identifies six dimensions in the analysis of digital twins:
Industrial Sectors Referenced in Digital Twin Applications
It was observed that Digital Twins are used in different industrial sectors. The identified industrial sectors where Digital Twins are applied are (ordered by count in parenthesis): manufacturing (54), aerospace (5), energy (4), automotive (3), marine (3), petroleum (2), agricultural (2), healthcare (2), public sector (1), and mining (1).
Purpose of Digital Twin Applications
The purpose dimension describes three different types of Digital Twin applications. The applications of Digital Twins have been divided into the following three purposes (ordered by count in parenthesis): simulation (47), monitoring (32), and control (23).
A specific Digital Twin application can be assigned to multiple purposes.
The simulation purpose contains applications where the behavior of physical objects can be reproduced in a virtual space. This allows planning or optimizing products or production plants without relying on the physical object.
The monitoring purpose includes all applications focusing on the representation of the current state and its interpretation of a physical object. The control purpose covers applications where Digital Twins directly influence products or manufacturing assets.
Physical Reference Objects of Digital Twins
The third dimension describes the physical reference object (Physical Twin), which is the physical counterpart of a Digital Twin. According to the definitions of Grieves (2014) and Tao et al. (2018), one main part of Digital Twins is the physical part. The following four categories of physical objects have been identified (ordered by count in parenthesis): manufacturing asset (45), product (27), human (2), and infrastructure (2). Augmented reality or virtual reality could be considered an additional category
Manufacturing assets are all machines and systems used within a production plant. Manufacturing assets stay in the same production line for most of their lifespan, such as a product manufactured in an assembly line
Products refer to physical products created by manufacturers to address the needs of their customers. In contrast to manufacturing assets, products will leave the area of influence of the producer at a certain point in their lifecycle. Hence, twins could be used to model the supply chain.
People could represent humans in manufacturing, smart cities, etc.
The idea of infrastructure could also include a system (smart cities) or a deployed physical product (wind turbines in production)
Completeness of Digital Twins
The dimension of completeness can be measured by the number of represented features of the physical object by the Digital Twin, for example, geometry, temperature, humidity, or power consumption.
Creation Time of Digital Twins
The creation time describes whether a Digital Twin is created before or after its physical counterpart. Creation time can be divided into two categories (count in parenthesis): Digital Twins can be created before the Physical Twin exists, i.e., a prototype (11), or at any later point during the existence of the
The connection between Digital and Physical Twin
The last identified dimension of Digital Twins is the connection between the Physical and the Digital Twin. According to the definitions of Grieves (2014) and Tao et al. (2018), the connection between the physical and virtual object is a mandatory part of a Digital Twin. However, in our research, we identified three manifestations of connection (amount in parenthesis): no connection (23) ex when the physical object does not exist, one-directional connection (39) ex when the twin is used for monitoring to predict failure, and bi-directional connection (25) ex when the digital twin needs to control the physical twin without human intervention.
Conclusion
As we see, the subject of digital twins is complex and multi-dimensional and impacts industries.
Dimensions of Digital Twin Applications – A Literature Review
Image source Siemens