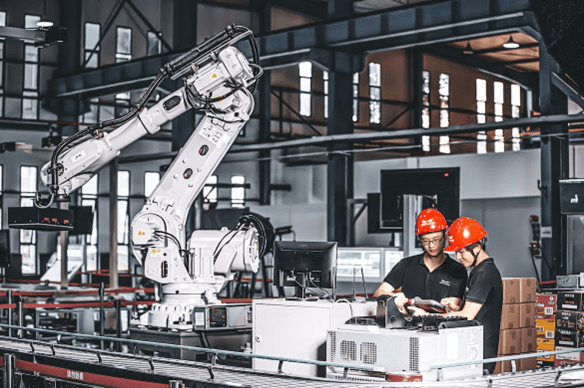
Manufacturers often turn to digitalization strategies to improve their competitiveness, address labor shortages, and boost productivity. These efforts are driven by a desire to stay ahead of the game rather than simply defend against the competition.
However, moving to the front foot regarding generated data unlocks waves of innovation — creating fast, bold, competitive, and agile organizations with increased production capacity and reduced operating costs.
Let’s look beyond the prosaic to three ways data collection can transform operations.
#1: Advanced analytics for patterns and relationships
Traditional yield management in business has relied on reducing production variability and waste through process improvements using Six Sigma or Lean. However, improving output while using the same or fewer inputs is influenced by countless variables — which can easily disrupt efforts, whether individually or combined.
The generated volume of shop-floor data is overwhelming for humans, yet it offers manufacturers profound insights. Advanced statistical analysis of manufacturing datasets allows businesses to seek patterns, sensitivities, and correlations between data that empower meaningful yield improvements. The following case study from a precious metals mine illustrates the possible gains.
A mine had experienced declining ore grades of 20% and sought ways to optimize its operation beyond simply speeding up the extraction process. The management implemented advanced analytics to analyze the huge number of variables and multiple pieces of equipment used in the mining process. The extraction process included grinding, cyanidation, oxidation, and leaching processes comprising multiple complex parameters.
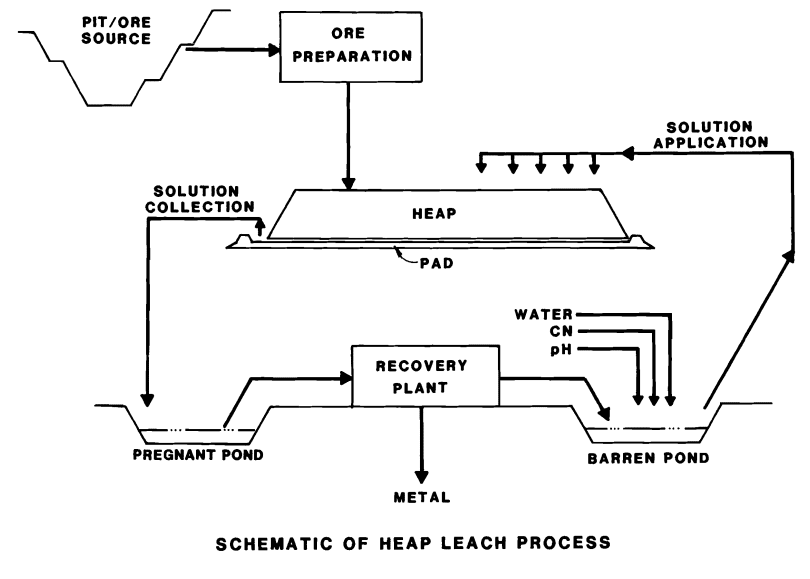
The analysis noticed one parameter central to the leaching process was dissolved oxygen, and it correlated oxygen concentration with fluctuations in process control. When oxygen levels peaked, the mine performance levels improved. From this insight, the team made some small adjustments to its leach-recovery process, which increased the average mine yield by 3.7% in three months. Without making capital investments or major changes, the mine increased its annual profit by between $10 million and $20 million.
#2: Use of ML and AI technologies
The availability of machine learning and artificial intelligence, coupled with an explosion in the industrial internet of things (IIoT) and edge computing, has revolutionized equipment maintenance.
Manufacturers in asset-intensive industries like oil and gas, mining, chemical, or pulp and paper are leading the charge in implementing machine learning capabilities for predictive maintenance (PdM) purposes. In these industries, critical asset failure has enormous consequences — impacting the safety of life, the environment, and financial viability.
Predictive maintenance allows maintenance professionals to target critical equipment. Predictive algorithms review and learn from historical operational data while monitoring real-time operations to identify deterioration in operating characteristics that indicate future failure. While the process is complex and takes time, it’s beneficial for manufacturers.
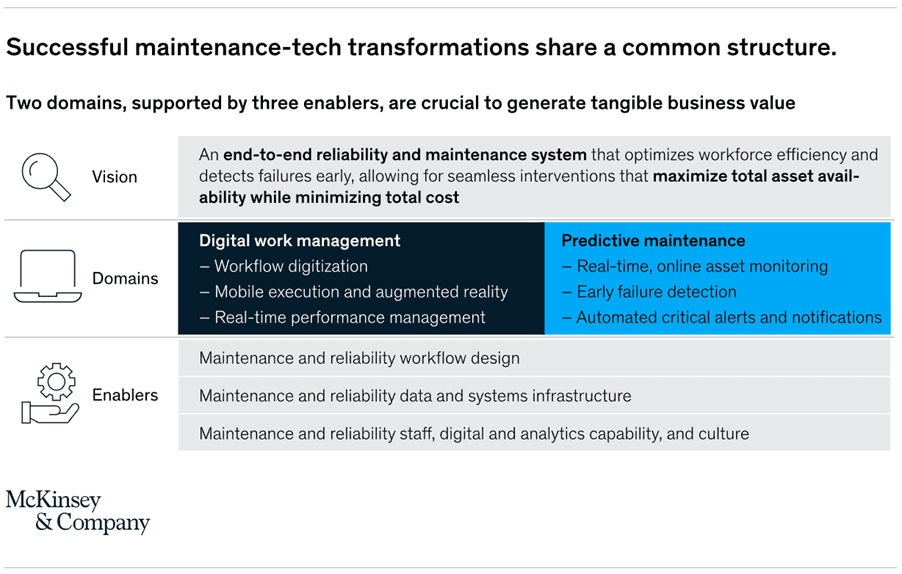
One large offshore oil and gas producer implemented PdM on nine offshore platforms. The effort began with identifying only critical equipment whose failure had major consequences. In this way, they could ensure an acceptable return on investment.
Training the analytics engine on data from 30 years of operation, data scientists built hundreds of advanced-analytic models and implemented a testing regime to reduce false positives to acceptable levels. The outcome was an average 20% reduction in downtime, increasing annual production by more than 500,000 barrels of oil.
#3: Full visibility into supply chains
A few years ago, a survey of 623 businesses found that almost 60% of firms believed their supply chain was a competitive advantage, and 77% claimed to spend between 5% and 15% of their turnover on supply chain issues.
Of their top five technology priorities, all were related to data management. When quizzed on their strategic priorities, the strategy of gaining full visibility into their supply chain had moved from 6th position in 2015 to 3rd position in 2017.
With the recent pandemic and global supply issues, one can only speculate where that priority now sits. The following graphic illustrates the degree of visibility the respondents felt they had in their supply chain.
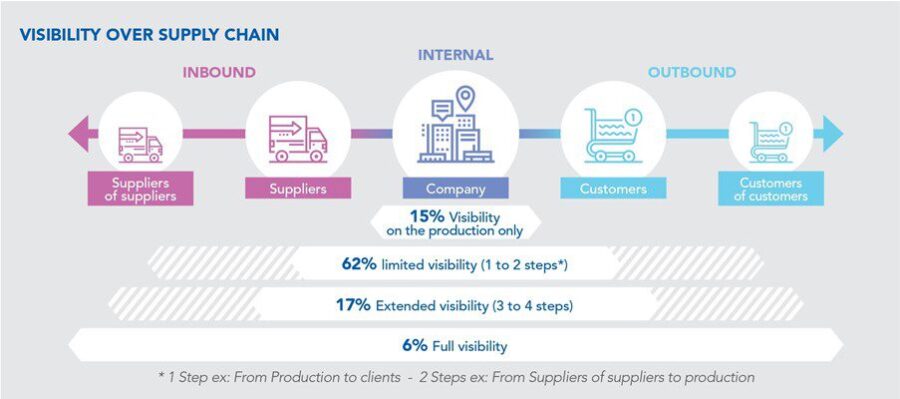
Exploiting big data provides end-to-end visibility into supply chains and supports greater automation, improved stakeholder relationships, and greater productivity and collaboration, allowing manufacturers to identify issues early and become more agile and proactive. FedEx handles over nine million shipments a day, and it’s realized the potential in the data such volumes create.
Rather than silo its efforts by focusing on spend analytics or demand planning, FedEx uses its huge volumes of unstructured data to provide more comprehensive insight. One outcome has been using GPS sensing devices and a web-based collaboration platform to track time-sensitive and high-value shipments.
The initiative allows trusted stakeholders to receive real-time alerts, analytics, and updates — giving precise locations, temperature readings, and advice when the shipment is opened. Deloitte Consulting’s experience suggests that such companies can realize increased margins of 2% to 4% by better analyzing their supply chain data.
Parting thoughts
Data collection and advanced analytics offer manufacturers far more than an opportunity to retain their competitive position. Correctly used, it can reinvent an organization, transforming supply chains and leveraging big data and predictive analytics to reimagine production while working smarter and more sustainably. While the process is unarguably complex and it can be time-consuming, the return on investment is a compelling argument for considering beginning the journey.
Bryan Christiansen is the founder and CEO of Limble CMMS. Limble is a modern, easy-to-use mobile CMMS software that takes the stress and chaos out of maintenance by helping managers organize, automate, and streamline their maintenance operations.